Как сделать станок для производства шлакоблока.
Шлакоблоками условно называются строительные блоки (стеновые камни) полученные методом вибропрессования раствора бетона в форме. Состав бетона при производстве шлакоблока: шлак, зола, отходы горения угля (других материалов). Но в процессе реального производства в состав шлакоблока могут входить любые наиболее доступные материалы в Вашем регионе – это может быть отсев щебня (камня, гранита), отходы кирпича, гравий, песок, опилки (после обработки), керамзит, перлит, песчано-гравийная смесь и многое другое.
Преимущества шлакоблоков перед другими строительными стеновыми материалами:
- дешевизна при возможности применения «подручного» материала и низкая себестоимость, если Вы захотите самостоятельно организовать изготовление шлакоблока;
- относительно высокая скорость постройки стен из шлакоблоков;
- из них просто построить малоэтажное (2-3 этажа) строение (гараж, дом, дачу, хозблок, мастерскую и т.п.) даже не прибегая к услугам каменщика. (1 блок = 3-4 кирпича);
- стены из шлакоблоков звуко- и тепло- не проницаемы;
- цена шлакоблока ниже цен на кирпич, пеноблок и других строительных материалов из-за дешевизны и доступности его компонентов.
На изготовление одного шлакоблока уходит 0,011 куб.м раствора, в пропорции 1:7 (цемент:граншлак), т.е. из одного мешка цемента, вы получите 36 готовых блоков. Себестоимость готового блока учитывая цены вашего региона, вы сможете подсчитать сами.
Ну а теперь я покажу и расскажу как я делал свой первый станок.
Теперь делаем короб вот размеры
....Теперь идем к токарю надо сделать 3 стакана и 6 пятаков,теперь все это...
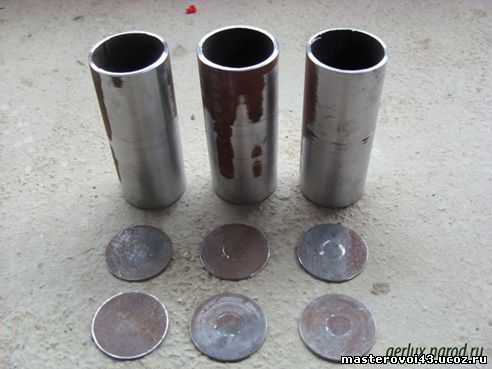
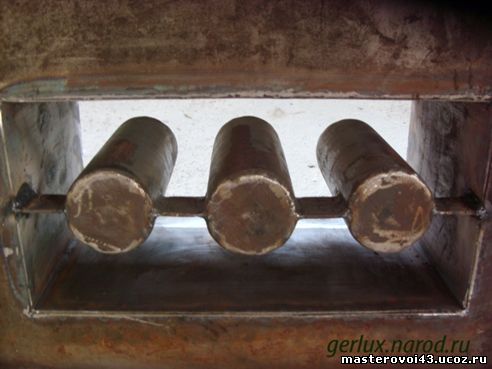
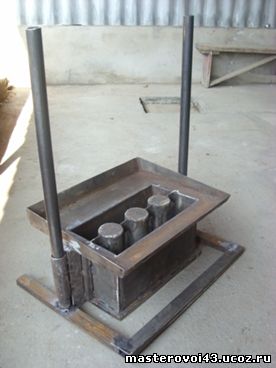
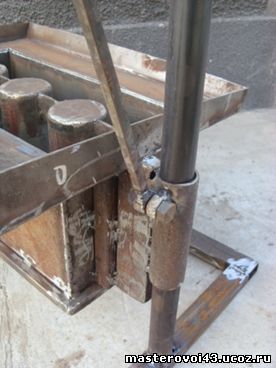
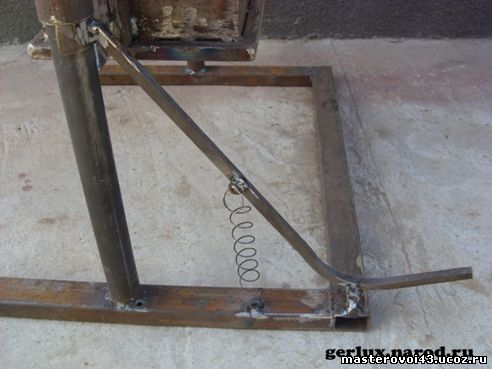
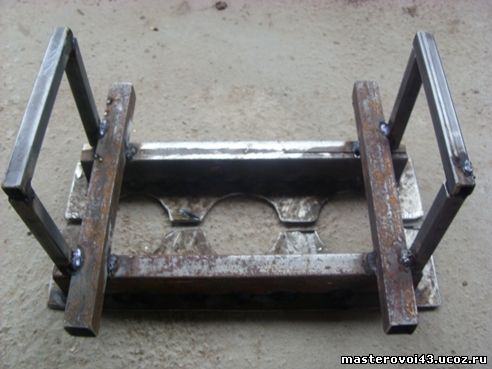
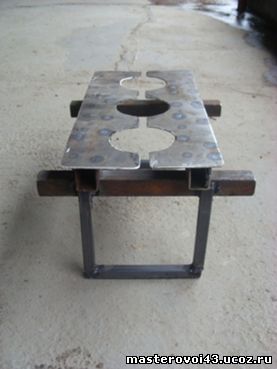
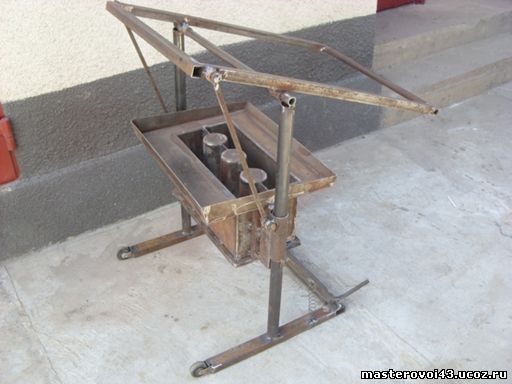
Что необходимо для производства строительных блоков?
Сырье. Для производства строительных блоков необходимы следующие компоненты:
цемент
наполнитель
пластифицирующая добавка (желательна)
вода
Цемент - марки 400. Возможен и другой. Но необходим подбор пропорций. Например, при использовании цемента марки 300, его расход следует увеличить на 10-15%.
Наполнителями для бетона могут быть самые разные материалы: песок, щебень, шлак, граншлак, зола, опилки, стружка, отсев, керамзит, гипс, лом кирпича и другие природные и производственные материалы.
В зависимости от местных условий, требований к производимым блокам и себестоимости, Вы можете выбрать соответствующий наполнитель.
Расскажу несколько составов бетона и основные группы бетонов.
Шлак с металлургических предприятий (серого или темно серого цвета с высоким содержанием цемента, сеянная мелкая фракция) — 9 частей
цемент — 1 часть
вода 0,5 объема цемента
Граншлак с металлургических предприятий (желто-зеленоватого) — 4 части
вода 0,5 объема цемента
Другие шлакобетоны
Бетоны на песке и щебнеБетон на отходах кирпича
мелкий отсев — 4 части
цемент — 1 часть
10. Керамзитобетон
11. Золобетон
12. Опилкобетон
13. Перлитобетон
14. Полистеролбетон и другие бетоны с разным сочетанием перечисленных.
Теперь понятно, что бытующее название «шлакоблок» не самое точное определение возможных строительных блоков.
Пластифицирующая добавка— это не обязательный компонент бетона.
Но ее технологическое применение обеспечивает:
раннюю прочность блоков (это очень важно при ограниченных производственных площадях),
повышает качество блоков (снижается трещинообразование и истираемость блоков),
улучшается водонепроницаемость и морозостойкость бетона.
повышается производительность.
Количество добавки очень незначительно — порядка 5 г на блок.
Далее будем называть ее Универсальная Пластифицирующая Добавка (УПД)
Технология изготовления строительных блоков:
Подготовка бетона
Производство блоков
Просушка и складирование готовых блоков.
Подготовка бетона (на примере ранее приведенного 2-го рецепта бетона):
Засыпаете 4 лопаты мелкого отсева + 4 лопаты гранулированного шлака;
Засыпаете 1 лопату цемента;
Тщательно перемешиваете;
Добавляете в воду растворенную УПД;
Перемешиваете. При этом бетон качественно пропитывается раствором УПД.
Производство блоков
Засыпаете в вибростанок бетон. Предварительная усадка (3сек. )
Устанавливаете прижим и включаете вибратор.
С вибрацией поднимаете станок — готовый блок остается на площадке.
Необходимый набор прочности шлакоблока (для складирования) происходит при естественной температуре от 36 до 96 часов (без применения специальных добавок - релаксол, фулерон и другие). Полное затвердевание шлакоблоков (или вибробетонных камней) происходит в течении месяца при температуре не менее 20 градусов и соблюдением условия высокой влажности. Это непременное условие, иначе процесс набора прочности шлакоблока может перейти в процесс "пересыхания" (сгорания), что приведёт к значительной потери прочности шлакоблока. Температура в помещении или на площадке для производства блоков должна быть от 1 градуса и выше. При использовании ускорителей схватывания бетона и более высокой окружающей температуре, изготовление шлакоблока происходит с ускоренным набором прочности. После этого шлакоблоки складируются, где происходит дальнейший набор прочности не менее 50% от проектного согласно ГОСТа для возможности отгрузки потребителю или применения на стройплощадке.
Среди всех недостатков шлакоблока перед другими строительными стеновыми материалами можно выделить сравнительно низкую прочность постройки стен из шлакоблоков.